Analysis of the price list and construction plan for the installation of Chinese grid steel structures
In the context of the booming development of the construction industry today, grid steel structures have been widely used in various large-scale building facilities due to their unique structural characteristics and aesthetics. Whether it's the grand dome of a sports stadium or the spacious architecture of an exhibition hall, they all rely on the presence of steel truss structures.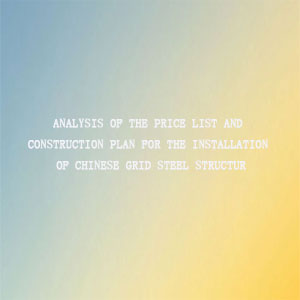
(1) Construction preparation
At the initial stage of project initiation, detailed construction preparation work is the cornerstone to ensure the smooth progress of the project. Firstly, a professional design team collaborates with the grid steel structure manufacturer to meticulously create a precise and detailed design blueprint based on the overall planning, functional positioning, and load-bearing requirements of the building. In this process, it is necessary to fully consider various factors such as the terrain and topography of the site, the impact of the surrounding environment, and the future usage needs of the building, to ensure the scientific and feasibility of the design scheme.
At the same time, the preparation work for materials is progressing synchronously. Grid steel structure manufacturers rely on their abundant resource channels and strict quality control systems to screen out high-quality materials that meet national standards and have excellent performance, such as common Q345B and other high-quality materials. In the procurement process, it is not only necessary to carefully verify key indicators such as material reports and mechanical properties of steel, but also to ensure that the supply quantity and supply cycle of materials can accurately match the project schedule, avoiding construction delays caused by material shortages or delays.
The preparation of the construction site cannot be ignored either. It is necessary to comprehensively clean and level the site, reasonably plan different functional areas such as material stacking area, processing and production area, and construction operation area, and build temporary office space, warehouse, and worker living facilities to create an orderly, convenient, and safe working environment for the construction team.
(2) Processing and manufacturing process
Processing and manufacturing are one of the core processes in the construction of grid steel structures, and their quality directly affects the stability and safety of the entire structure. In the cutting and cutting process, advanced CNC cutting equipment such as high-precision plasma cutting machines or laser cutting machines are used to precisely cut the steel according to the size requirements specified in the design drawings, controlling the length error of the rod within a very small range and the angular deviation almost zero, thus laying a solid foundation for subsequent assembly work.
Welding operations require a team of skilled and experienced welders who are proficient in using advanced welding techniques such as carbon dioxide gas shielded welding to ensure that each weld seam is uniform, full, and free of defects such as porosity and slag inclusion. The welding strength fully meets the design standards. During the assembly phase, depending on the specific structural form and scale of the grid, the ground assembly or block assembly method can be flexibly selected. With the help of professionally designed and manufactured fixtures, the relative positions of each member and node are effectively ensured to be precise and error free during the assembly process, enabling the entire grid structure to have extremely high precision and stability before installation.
To enhance the durability and corrosion resistance of the grid steel structure, a comprehensive and systematic anti-corrosion and coating treatment is required after processing and manufacturing. Firstly, the surface of the steel should be thoroughly derusted, using efficient methods such as sandblasting or shot blasting to remove the oxide scale and rust on the surface of the steel, giving it a metallic luster. Subsequently, the primer, intermediate coat, and topcoat are applied sequentially. Depending on the different environments of the project, such as coastal areas, industrial pollution areas, or ordinary inland areas, appropriate anti-corrosion coating brands and models are selected to ensure that the grid steel structure can effectively resist external environmental erosion during long-term use.
(3) Installation method
1. Full house scaffolding method: This method is suitable for the installation of small or relatively regular shaped grid structures. By setting up a full scaffold on the construction site, a stable operating platform is provided for construction personnel to gradually assemble grid members and nodes on the scaffold. Although this method has the advantages of good construction process stability and relatively simple operation, the overall cost is relatively high due to the large workload of scaffolding construction, high material rental costs, and long construction period.
2. Slip method: For large-span truss steel structures, slip method is a relatively efficient installation method. The principle is to first assemble the grid into several larger units on the ground, and then lay sliding tracks on the construction site, equipped with professional traction equipment. During installation, use traction equipment to gradually slide the assembled units along the sliding track to the designated design position. This method significantly reduces the amount of high-altitude work, effectively improves construction efficiency, and reduces construction safety risks. However, the sliding method requires high installation accuracy of the sliding track, performance of the traction equipment, and technical level of the construction team. The initial equipment investment and track laying cost should not be underestimated.
3. Integral jacking method: When the construction site conditions are limited and it is difficult to carry out large-scale ground assembly operations, integral jacking method becomes a feasible choice. This method involves setting up a lifting device at the center or specific position of the grid structure, and gradually lifting the grid into place through hydraulic jacks and other lifting equipment. During the lifting process, high-precision monitoring instruments are needed to monitor the lifting speed, synchronization, and deformation of the grid structure in real time, ensuring the safety, smoothness, and accuracy of the lifting process. The overall lifting method is technically difficult and requires extremely high reliability and stability of the lifting equipment, but it can play a unique advantage in specific engineering scenarios.
2、 Price List for Installation of Grid Steel Structure**
(1) Material cost
Steel, as the main raw material for grid steel structures, has a significant impact on installation prices due to price fluctuations. The price of steel is influenced by a combination of factors such as market supply and demand, international raw material market dynamics, and domestic macroeconomic conditions. When formulating installation prices for grid steel structures, manufacturers will accurately calculate material costs based on the specific specifications of the steel required for the project (such as the diameter and wall thickness of the members), materials (such as Q345B, Q235B, and other different strength grades), and the current market price of the steel. Generally speaking, the proportion of material cost in the total installation price of grid steel structures fluctuates between 40% and 60%, depending on factors such as the scale of the project, steel selection standards, and market price trends.
(2) Processing and production costs
The processing and manufacturing costs cover the labor costs and equipment depreciation expenses incurred in a series of processes from steel cutting and cutting to welding, assembly, and anti-corrosion coating. In the cutting and cutting process, although the use of advanced CNC equipment has improved cutting accuracy and efficiency, the purchase and maintenance costs of the equipment are also correspondingly high, and these costs will be shared among each processed grid structure. The welding and assembly process requires the participation of a large number of skilled technicians, and their labor wages vary depending on regional differences and technical levels. In the anti-corrosion coating process, the procurement cost of coatings and the operating cost of coating equipment also constitute a part of the processing and manufacturing costs. Overall, the cost of processing and manufacturing accounts for about 20% -30% of the total installation price of grid steel structures, and its specific proportion is affected by factors such as the complexity of processing technology, the size of processing volume, and regional labor cost differences.
(3) Installation cost
Different installation methods correspond to different installation costs. As mentioned earlier, the full house scaffolding method has relatively high installation costs due to the high cost of scaffolding construction and long construction period; Although the sliding method has improved construction efficiency to a certain extent, the installation cost is not low due to the high rental and track laying costs of sliding equipment; Due to the high technical difficulty and equipment requirements, the installation cost of the overall lifting method also accounts for a significant proportion. The installation cost accounts for approximately 10% -20% of the total installation price of the grid steel structure, depending on factors such as the difficulty of installation, the choice of installation method, the professional level of the construction team, and market conditions.
(4) Transportation costs
The transportation cost incurred during the process of transporting the grid steel structure processed and manufactured in the factory to the construction site is also an important component of the installation price. The transportation cost is mainly influenced by factors such as the distance of transportation, the choice of transportation mode (such as road transportation, railway transportation, or waterway transportation), and the volume and weight of the grid structure. For grid structures that are far away, bulky, and heavy in weight, transportation costs may significantly increase. Generally speaking, transportation costs account for 3% -8% of the total installation price of grid steel structures, and the specific situation needs to be calculated in detail according to the actual transportation needs of the project.
(5) Other expenses
In addition to the main cost items mentioned above, the installation price of the grid steel structure also includes some other costs, such as design fees, engineering inspection fees, and project management fees. Design fees are fees charged by a professional design team for providing design services to a project, and their amount depends on the complexity of the design and the team's reputation and professional level; The engineering inspection cost is used to inspect the quality of the grid structure during the construction process, such as weld seam inspection, steel mechanical performance testing, etc., to ensure that the engineering quality meets relevant standards and specifications; Project management costs cover the entire process from project planning, organization and implementation to completion and acceptance, including management personnel salaries, office expenses, etc. These other costs account for approximately 5% -10% of the total price for the installation of the grid steel structure.
In summary, the installation price and construction plan of Chinese grid steel structures are a complex and interrelated system. In actual engineering projects, when choosing a steel frame structure manufacturer, the owner or investor should not only focus on price factors, but also consider multiple factors such as the manufacturer's technical strength, construction experience, past engineering performance, and after-sales service. Only in this way can we ensure that the grid steel structure project can efficiently and smoothly complete the construction task while ensuring quality and safety, and play its due structural functions and economic benefits within the expected service life.