The difference between aluminum zinc and galvanized layer about ppgi
In the construction of steel structure factory buildings, the coating quality of color steel plates is directly related to the durability, protective performance and appearance maintenance of the factory buildings. Galvanizing and aluminum-zinc plating are two common coating treatments for color steel plates. They are significantly different in many aspects. These differences are crucial to determine their applicability in different acid and alkali environments.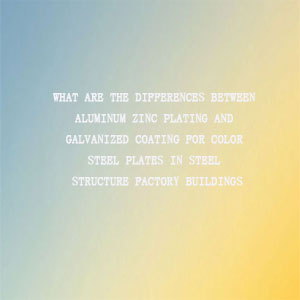
1. Parameters
The thickness of galvanized coating is usually measured by the amount of zinc coating per square meter. Common specifications include 60g/m², 80g/m², 120g/m², 275g/m² and other different specifications. For example, steel structure factories in some mildly corrosive environments may use 80g/m² - 120g/m² galvanizing, while for factories with harsher environments or longer service life requirements, 275g/m² galvanizing may be used. quantity.
2. Advantages and Disadvantages
- advantage:
- Cost-effectiveness: The galvanizing process is relatively mature and the cost of raw materials is relatively low, which gives galvanized color steel plates a clear advantage in price. It is an economical and affordable choice for some steel structure factory building projects with limited budget and not particularly high protection performance requirements.
- Initial protection: The zinc layer can form a physical barrier on the surface of the steel plate, effectively blocking oxygen and moisture in the air, preventing the steel plate from direct contact with corrosive media, playing a good protective role in the early stage of the steel plate, and delaying the process of steel plate rusting. .
- shortcoming:
- Limitation of corrosion resistance: In harsh environments, especially in acid and alkali environments, the corrosion resistance of the galvanized layer is poor. Zinc is prone to chemical reactions in acidic or alkaline solutions and is dissolved, causing damage to the coating and exposing the steel plate to a corrosive environment.
- Vulnerable appearance: With the passage of time and environmental effects, the galvanized layer will gradually oxidize and corrode, resulting in changes in the appearance of the color steel plate, such as blurring of the zinc, darkening of the surface, rust spots, etc., affecting the quality of the steel structure factory building. Overall aesthetics.
3. Performance
- Anti-corrosion performance: In a neutral atmospheric environment, the galvanized layer relies on its own sacrificial anode protection principle to provide anti-corrosion protection for the steel plate for a certain period of time. When the surface of the steel plate is damaged, the zinc layer will corrode preferentially, thereby protecting the main body of the steel plate. However, in an acidic or alkaline environment, this protective effect will be greatly reduced, because zinc will react rapidly with acids or alkali to form soluble salts, causing the coating to lose its protective ability.
- Processing performance: Galvanized steel sheets have good processing properties and are easy to perform cutting, bending, stamping and other processing operations. During the processing, the galvanized layer has little impact on the processing technology, which can ensure that the dimensional accuracy and shape of the processed color steel plates meet the requirements, making it convenient for installation and construction in the construction of Steel structure workshops.
- Welding performance: Due to the low melting point of zinc, when welding galvanized steel sheets, the high temperature will quickly melt and evaporate the zinc, producing zinc vapor. If these zinc vapors cannot be discharged in time, defects such as pores and slag inclusions may be formed in the weld, affecting the welding quality. Therefore, special welding processes are required when welding galvanized steel sheets, such as removing the zinc layer at the welding site in advance or using appropriate welding parameters and welding materials.
4. Application environment
Galvanized color steel plates are suitable for steel structure factories in inland areas where the environment is relatively mild and there is no strong acid or alkali pollution. For example, ordinary small industrial plants, warehouses, simple agricultural production facilities, etc. In these environments, the galvanized layer can meet basic protection needs and can guarantee a service life of 5-10 years under normal use conditions. In terms of acid and alkali environments, galvanized color steel plates are not suitable for highly acidic or alkaline environments, such as chemical production workshops, electroplating plants, sewage treatment plants and other places.
2. Aluminum zinc coating
1. Parameters
Galvalume coating is an alloy coating composed of approximately 55% aluminum, 43.4% zinc and 1.6% silicon. The coating thickness is also expressed in weight per square meter, and common ones are 150g/m², 180g/m², 200g/m², etc. In steel structure factories with high protective performance requirements, especially in coastal areas or areas with serious industrial pollution, galvanized steel sheets with a concentration of 180g/m² or more are usually used.
2. Advantages and Disadvantages
- advantage:
- Super corrosion resistance: The aluminum in the galvanized layer can quickly form a dense aluminum oxide protective film in the air. This film has good chemical stability and can effectively block external corrosive media. At the same time, the sacrificial anode protection effect of zinc also enhances the overall protective effect to a certain extent. In acidic and alkaline environments, the corrosion resistance of aluminum-zinc coating is significantly improved compared to zinc coating. In an acidic environment, aluminum oxides and hydroxides can neutralize acidic substances to a certain extent and slow down the corrosion rate; in an alkaline environment, the alloy structure of aluminum and zinc is relatively stable and is not easily corroded by alkaline substances.
- Good appearance stability: The appearance of galvanized steel plates can maintain good stability during long-term use. Due to the existence of the aluminum oxide protective film, the surface of the color steel plate is not prone to oxidation, discoloration and other phenomena, and can maintain a good appearance effect for a long time. For some steel structure factories that have higher requirements for appearance, such as factory buildings in commercial buildings or modern buildings The industrial park factory has great advantages.
- shortcoming:
- Higher cost: The production process of galvanized steel is relatively complex, requires more advanced equipment and technology, and the cost of raw materials is high. This results in a relatively high price of galvanized steel sheets, which limits its wide application to a certain extent. , especially in some projects with strict cost control.
- Increased processing difficulty: The hardness of the galvanized layer is relatively high. When performing some complex processing operations, such as deep bending, stamping, etc., the coating is prone to cracking or falling off. This requires the use of more precise processing equipment and strict processing technology control when processing galvanized steel plates, which increases processing costs and processing difficulty.
3. Performance
- Anti-corrosion performance: In harsh marine climate (high salt spray), industrial pollution (containing acid and alkali gases) and other environments, the galvanized layer shows excellent corrosion resistance. Even if the coating is partially damaged, the surrounding aluminum-zinc alloy can still play a good protective role and prevent the steel plate from rusting. In acidic environments, its corrosion resistance is several times higher than that of galvanized layers, and it can also maintain relatively stable protective performance in alkaline environments.
- Processing performance: Although it is difficult to process galvanized steel sheets, conventional processing operations can still be performed by using appropriate processing techniques and equipment, such as adjusting the bending radius, controlling the stamping force, etc. However, more attention needs to be paid to protecting the coating during processing to avoid damaging the integrity of the coating due to improper processing.
- Welding performance: Al-zinc color steel plate faces similar zinc vapor problems as galvanized steel plate when welding, and due to the complex composition of its coating, welding is more difficult. Special welding processes are required, such as pulse welding technology, pre-welding treatment (such as grinding to remove part of the coating), etc., to ensure welding quality, reduce the occurrence of welding defects, and ensure the strength and sealing of the weld.
4. Application environment
Galvalume-coated steel sheets are suitable for coastal areas, chemical industry parks, areas with serious industrial pollution, and steel structure factories with high requirements on appearance and durability. In coastal areas, it can effectively resist the erosion of high humidity and strong salt spray; in chemical industry parks and other environments with acid and alkali pollution, it can provide reliable protection for factories. For example, large chemical production plants, coastal logistics warehouses, modern industrial manufacturing plants, etc. In terms of acid and alkali environments, galvanized steel sheets can be used in a certain degree of acidic and alkaline environments. Compared with galvanized color steel sheets, they have wider applicability and their service life can reach 15-20 years in harsh environments. Even longer.
To sum up, when choosing color steel plate coating for steel structure factories, it is necessary to comprehensively consider various factors such as the geographical location of the factory, the use environment (especially acid and alkali environments), budget, and appearance requirements. If the factory is located in a mild inland environment and has a limited budget, galvanized color steel plates can meet the basic needs; if it is located in harsh environments such as coastal areas and chemical industries or has higher requirements for appearance and durability, galvanized color steel plates are more suitable.
From a single perspective, the coating of galvanized color steel plate is mainly zinc. Common coating amounts are various, low cost and good processability. However, it has weak acid and alkali corrosion resistance, especially in acidic environments. It is easily corroded. It is mostly suitable for inland mild environments. . Galvalume-coated steel sheets contain about 55% aluminum, about 43.4% zinc, and about 1.6% silicon. The coating amounts are available in various specifications. Its advantages are strong corrosion resistance, better performance than galvanizing in acid and alkali environments, and good appearance stability, but the cost is high and processing is difficult. It is more suitable for harsh or appearance-requiring environments such as coastal areas and chemical industrial parks, and has good adaptability in acidic and alkaline environments.
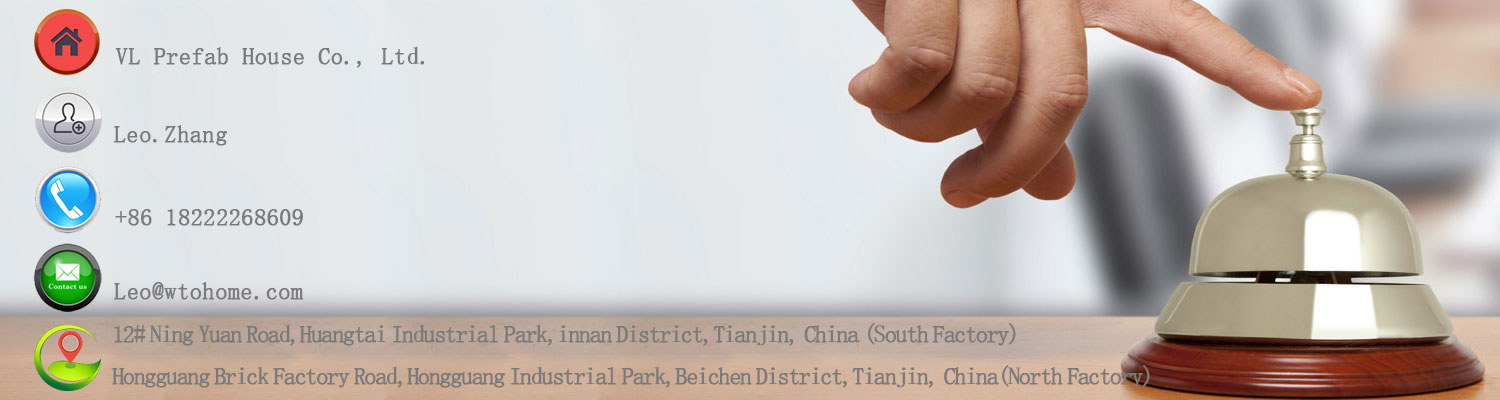